Sharpening our
operational edge
Delivering exceptional operational performance is essential to our long-term success. To accomplish this, we blend efficient personnel involvement with strategic use of Kaizen and Lean techniques, all under the guidance of a dedicated and knowledgeable leadership team. We take careful measures to enhance our abilities, ensuring we remain ahead of the competition.
Implementing the 6S Strategy
We have implemented the ‘6S’ strategy, which includes 5S and safety, across all our focus areas. We have divided each factory into zones with designated ownership, and there’s a 5S manual available. We conduct periodic red tag campaigns, and 6S is implemented in our shop floor, office areas, and even at our workers’ homes. Our efforts have created a conducive environment for achieving excellence within our factory premises. We conduct regular 5S audits, and the score is a part of the Balanced Score Card (BSC)/Key Result Area (KRA) for management staff. We are proud recipients of the 5S Excellence Trophy awarded by the CII.
Kaizen Journey
Our Company is committed to eliminating eight types of wastes (Mudas) by implementing Kaizen methodology. These include overproduction, waiting, motion, transportation, inventory, defects, over-processing, and unused skills. We have established an online Kaizen portal with a horizontal deployment feature to support this effort, enabling the successful replication of relevant Kaizens across different locations. Our coordinators evaluate and categorise Kaizens into levels I, II, and III, based on their impact on PQCDSHM (Productivity, Quality, Cost, Delivery, Safety, Health, and Morale), low investment, originality, root cause elimination, and other factors. We offer monetary awards for each location’s top three Kaizens per month, along with Kaizen certificates signed by our Vice President. Additionally, we recognise the location/employee with the most number of Kaizens at our annual Steel conference with the Kaizen Spark award. These recognitions serve to encourage a culture of Kaizen within our organisation.
Visual Factory
As part of our Total Productive Maintenance (TPM) efforts, we introduced visual control and management processes in all shop floors. To facilitate ease of understanding and compliance, we have converted all Standard Operating Procedures (SOPs) from English to local languages and have incorporated pictorial and video-based SOPs.
Total Productive Maintenance (TPM)
Our Company’s aim is to attain the ‘4 Zeros’ - Zero Accident, Zero Defect, Zero Waste, and Zero Breakdown - through the implementation of Total Productive Maintenance (TPM). This has resulted in significant improvements in Overall Equipment Effectiveness and in Productivity, Quality, Cost, Delivery, Safety, and Morale. By effectively implementing TPM, we have created a cultural shift from the traditional ‘I operate, You troubleshoot’ mindset to ‘I operate, I troubleshoot’ approach. Our Kanhe and Nashik plants have been certified for TPM Excellence, and we have initiated the certification process for our Bhopal and Vadodara plants. Following the successful attainment of ‘TPM Excellence’, our Nashik plant is now preparing for the ‘TPM Consistency’ award. We have also developed a roadmap for TPM certification across all our remaining plants.
Innovation-Led Progress
Mahindra Accelo Group strongly emphasises innovation, driven by our proprietary MIND™ (Mahindra INnovation methoD) approach. To enable the successful implementation of MIND™, our team received extensive training from a specialised team from M&M’s innovation cell. The training workshop included both theoretical and practical elements of innovation implementation. As a result of our focus on innovation, our submission for the Mahindra Innovation Award in FY 2022-23, titled ‘Job Height Measurement on Load’ using Linear Variable Differentiable Transformer (LVDT) at our Kanhe plant, was a finalist.
Six Sigma
In 2017, we embarked on our Six Sigma journey by providing our employees with a comprehensive nine-day training programme on Six Sigma theory. The training was based on the Six Sigma Green Belt module of the American Society for Quality (ASQ) syllabus and was designed to be rigorous and thorough. During the year under review, we trained four batches of employees from Kanhe, Bhopal, Chakan, Vadodara, and Nashik, with two batches at Chakan, one at Kanhe, and one at Vadodara.
3,020
Kaizens completed across all locations in FY 2022-23
100%
Participation obtained for Kaizen implementation
4
Innovation projects
completed
3
Innovation projects in-progress
124
Trained Green Belts since 2017
₹ 2.24 crore+
Cumulative savings
Strengthening Our Safety Culture
We have implemented The Mahindra Safety Way (TMSW) model, which is a comprehensive approach to safety at all of our Accelo plants. This model consists of 25 process parameters and 8 result parameters, as per the guidance of the Central Safety Council. As a result of our proactive safety approach, we had zero reportable and non-reportable accidents across all of our plants and locations in FY 2022-23. To monitor the safety of all employees, we have also implemented a departmental safety score methodology. Furthermore, all safety audits conducted thus far have not observed any serious or critical safety concerns.
ISO Certifications
All our plants are ISO 9001: 2015, ISO 14001: 2015 and ISO 45001: 2018 certified by TUV NORD, while our Chakan and Chennai plants are IATF 16949: 2016 certified. Kanhe plant completed the IATF assessment successfully by Bureau Veritas. These certifications have helped institutionalise robust processes and systems into our operations.
Value Stream Mapping (VSM)
We perform VSM by first calculating the Takt time, representing the customer demand time. Next, we map out the process from the supplier to the customer. During this process, we identify value-added and non-value-added activities and establish timelines for each. We then convert internal activities into external ones, while eliminating non-value-added activities. VSM projects were successfully implemented at both our shearing and die-casting lines, significantly improving our Process Cycle Efficiency (PCE). As a result, we enhanced our delivery performance in line with our customer requirements.
Single Minute Exchange of Die (SMED)
Our slitting lines have undergone successful SMED implementation. We utilised the Elimination, Combine, Realignment and Simplify (ECRS) principle to achieve this. As a result, we have significantly reduced the time taken to load and unload the die from several minutes to a single digit.
The Mahindra Way (TMW)
The Mahindra Group’s business excellence model The Mahindra Way (TMW) helps us to implement and promote comprehensive quality management through prioritised, systematic and continuous improvement, along with the application of Group Common Policies and Practices. In our pursuit of moving towards operational excellence, we have been promoted to Stage 6 in TMW Assessment. Very few companies across the Mahindra Group have been able to reach Stage 6.
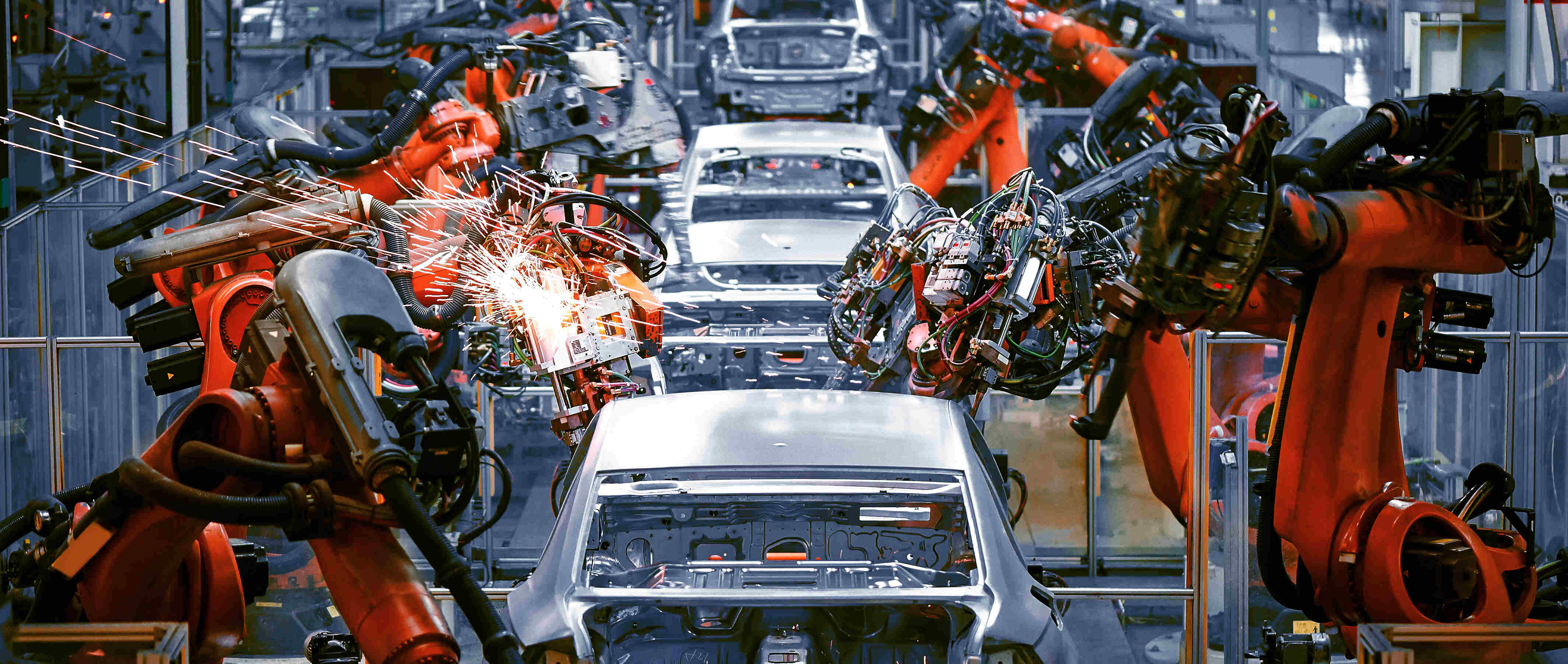
Safety Audits Conducted
- TMSW by CSC assessors
- IS14489 by DISH-approved auditor
- ISO 45001 by TUV Nord
- Internal safety audits