Adopting digitisation
across the
value chain
We are committed to strengthening our digital platforms that improve the execution process for both our customers and internal operations. These platforms aim to enhance efficiency and convenience significantly for all stakeholders involved. Currently, we have several applications in place that serve critical functions, and we have several more in the pipeline set to launch in the coming year.
Digital roll-out dashboard
Stage
|
Operation & Supply Chain
|
Finance & Accounting
|
Human Resources
|
Other Processes & Reporting
|
Total
|
---|---|---|---|---|---|
Deployed | 27 | 11 | 1 | 4 | 43 |
Under Development | 6 | 2 | 1 | 1 | 9 |
Planned | 4 | 4 | 1 | 10 | |
Total | 37 | 17 | 2 | 6 | 62 |
MRP Report
Need
The maintenance of raw material planning in an excel sheet has led to instances of excess or shortage of RM stock and numerous open purchase orders in the system.
Solution
We have recently introduced an MRP report that provides a comprehensive view of the status of raw materials, including MRP, GRN pending, stock at job workers, inventory, and indicators based on material MRP. With access to all the necessary details, open purchase orders can be closed on time, leading to better control over stocks.
Result
By achieving just-in-time stock with proper usage, we can effectively control overstocking. This leads to significant time savings in raw material planning, as we will only order the required amount of material when needed rather than ordering in bulk and storing excess inventory.
PDC Unlock Screen and PDC Details Uploading in SAP
Need
In the past, approvals were obtained manually and then had to be manually updated across individual invoices. This process also had to be replicated in PDC across all bills in SAP, which was time-consuming and caused delays. As a result, the sales team had to send approval request emails, resulting in trucks being held up.
Solution
We have developed an application that displays all data on one screen. When approved by the assigned approver, all invoices are unlocked within seconds. Additionally, PDC upload in SAP can now be done through an excel file.
Result
This new system has resulted in significant time savings-an estimated 3 minutes per transaction. This includes time saved on PDC approval, which previously amounted to 14 per day, and PDC updates, which amounted to 40 transactions.
Production Slitting Screen
Need
In the past, slitting calculations were done in Excel and manually transferred to the SAP system. Furthermore, the production process was not structured based on a Bill of Materials (BOM).
Solution
Our new system provides all the necessary checks and balances, ensuring input matches output. We can also easily calculate the required quantity based on the width entered, resulting in significant time savings. Furthermore, this screen is user-friendly and can be operated by machine operators as well.
Result
Implementing this new system has resulted in significant time savings, with an estimated 10 minutes saved per transaction, equating to approximately 1 minute per transaction, as we typically perform around 50 transactions daily.
Learning Management System (LMS)-SAP Integrations
Need
Previously, Vendor codes and Materials had to be created manually, which took approximately two days to complete for each vendor. PO/GR/Bill passing, we had to download all the relevant data into an Excel file and manually enter the information into the SAP system.
Solution
We have implemented a fully integrated system between the LMS (CERO Customer platform) and SAP using APIs. This system now includes automatic vendor and material creation, as well as automatic PO/GR/bill passing and advance payment processing.
Result
With the implementation of this fully integrated system, we have achieved significant time savings, with an estimated 10 minutes saved per transaction, which now takes approximately 1 minute to complete. Additionally, manual intervention is no longer needed, resulting in a much smoother and more streamlined process. We typically perform around 70 transactions per day, making this a significant improvement in efficiency.
Material Creation
Need
Previously, users had to manually create material codes one by one across all plants, which was both time-consuming and prone to errors.
Solution
With the implementation of this programme, we can now create up to 500 new materials in the system at once, resulting in significant time savings and significantly reducing the risk of errors.
Result
The implementation of this programme has resulted in significant time savings, with an estimated 20 minutes saved per transaction, which now takes approximately 1 minute to complete. We typically create around 30 new materials per day, making this a significant improvement in efficiency.
Invoicing (Delivery/PGI/Invoice in One Step)
Need
Previously, the process for completing this task involved three separate steps and also required manual input for batch placement, resulting in a time-consuming process.
Solution
Implementing this programme has resulted in a much more streamlined and efficient process for invoicing. Users can now enter all the relevant details for invoicing, including transport details, batch selection, and packing materials, all on a single screen. This information is then linked to the despatch screen, allowing for a continuous flow of information, resulting in significant time savings and significantly reducing the risk of errors.
Result
The implementation of this programme has resulted in significant time savings, with an estimated 10 minutes saved per transaction, which now takes approximately 1 minute to complete. As we perform approximately 1,300 transactions per day, this immensely improves efficiency. Having all the relevant data on a single screen has further improved our ability to process transactions quickly and accurately.
Hyperion Step Consolidation
Production Planning
By implementing MRP-based production planning, we can reduce manual efforts and minimise our dependency on manual labour. This helped us maintain a proper inventory of finished goods and restrict excess production above the maximum level defined in our SAP system. Ultimately, this will lead to a more streamlined and efficient production process, allowing us to better meet customer demands, while maximising our resources.
Production Declaration
With the introduction of an automated system for scrap entry, we can eliminate the need for manual calculations, including profile design scrap. This will significantly reduce errors in declaration entry in our SAP system, improving the accuracy of our records. We have further implemented the FG stick printing to streamline the process even further. A detailed analysis of data will be available for scrap reconciliation, enabling us to identify and address any actual or theoretical differences. This will lead to a more efficient and effective system for scrap management, saving time and reducing the risk of errors.
Result
By using this program, we can save around 5-6 minutes per coil declaration in SAP, which adds up to approximately 40 transactions per day.
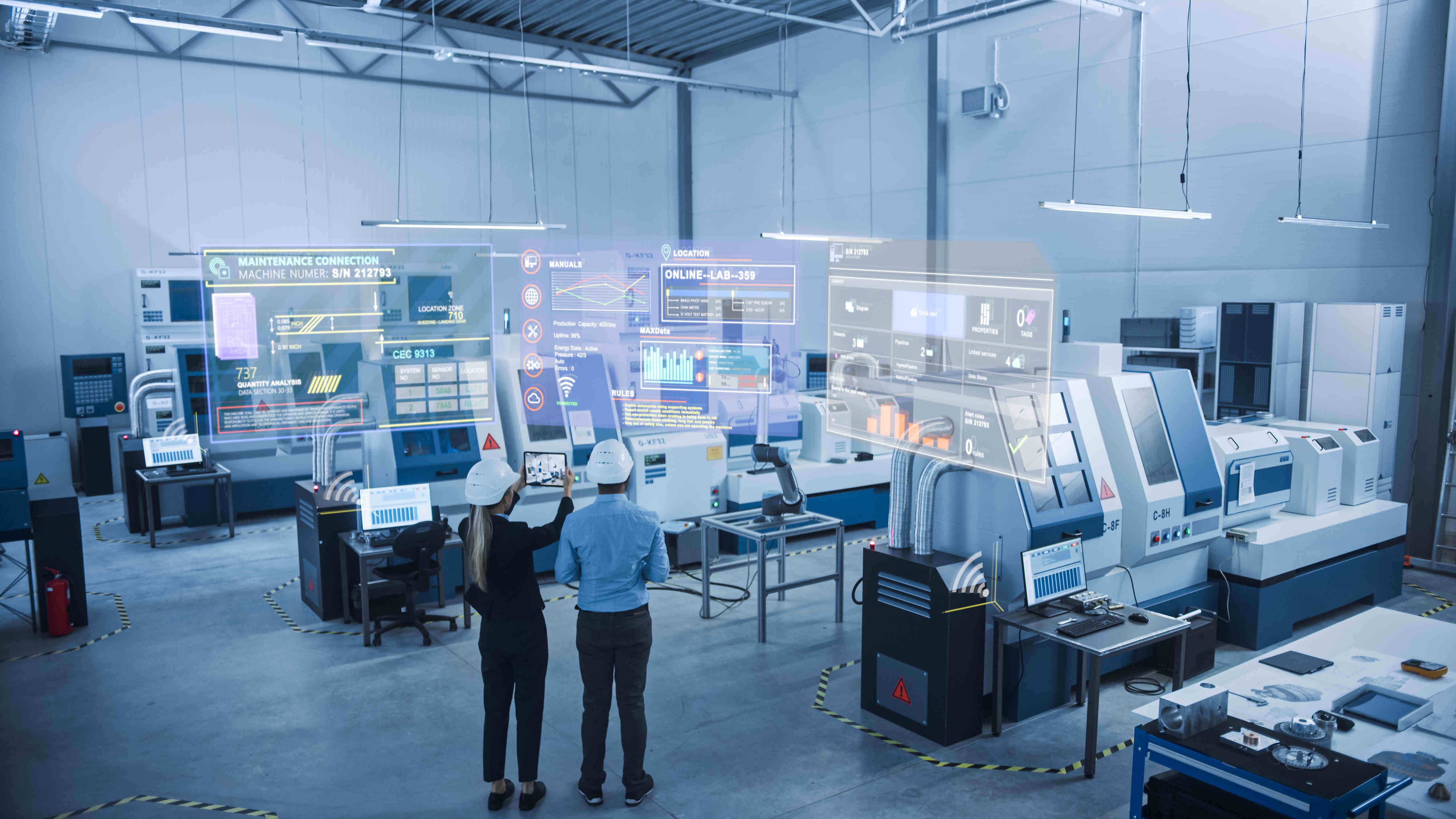
Inventory App
Need
Stock take was previously done manually, where an SAP Excel dump was printed on paper and updated in an Excel sheet for reconciliation. This process took approximately two days to complete and required around 20 officers.
Solution
Developed an Inventory App that streamlines the stock take process. Using the app, one person can scan the QR code of each material, with the capacity to scan up to 900 materials in just one hour. The app also features an automatic reconciliation process, eliminating the need for manual updates on an Excel sheet. This saves time and reduces the number of officers needed for the stock take, making the process more efficient.
Result
Stock take reduced from 2 days to 1 hour (4 transactions per year across 10 plants) with the help of the Inventory App developed, which enables a single person to scan the QR code and conduct the stock take with auto reconciliation.
Robotic Process Automation (RPA)
Need
For some tractions, users had to generate reports periodically which was a repetitive and time-consuming job. It also created a dependency on specific individuals.
Solution
RPA or Robotic Process Automation is a technology that uses software robots to automate repetitive, rule-based tasks. Implementing RPA eliminates the need for manual intervention, reduces errors, and increases efficiency. In our organisation, we have developed various RPAs to automate the following processes:
1.Auto Stock/Despatch report: The system automatically triggers mails for this report, which helps us control inventory.
2.Vehicle-wise Analysis & Realisation Report: The executable RPA generates this report, providing detailed analysis and realisation of vehicle-wise data.
By implementing these RPAs, we have reduced the manual efforts and made the process more efficient. There is no dependency on any individual, and the reports are generated automatically, saving time and reducing errors.
Result
Implementation of RPA has helped us save 2 hours more daily/weekly.